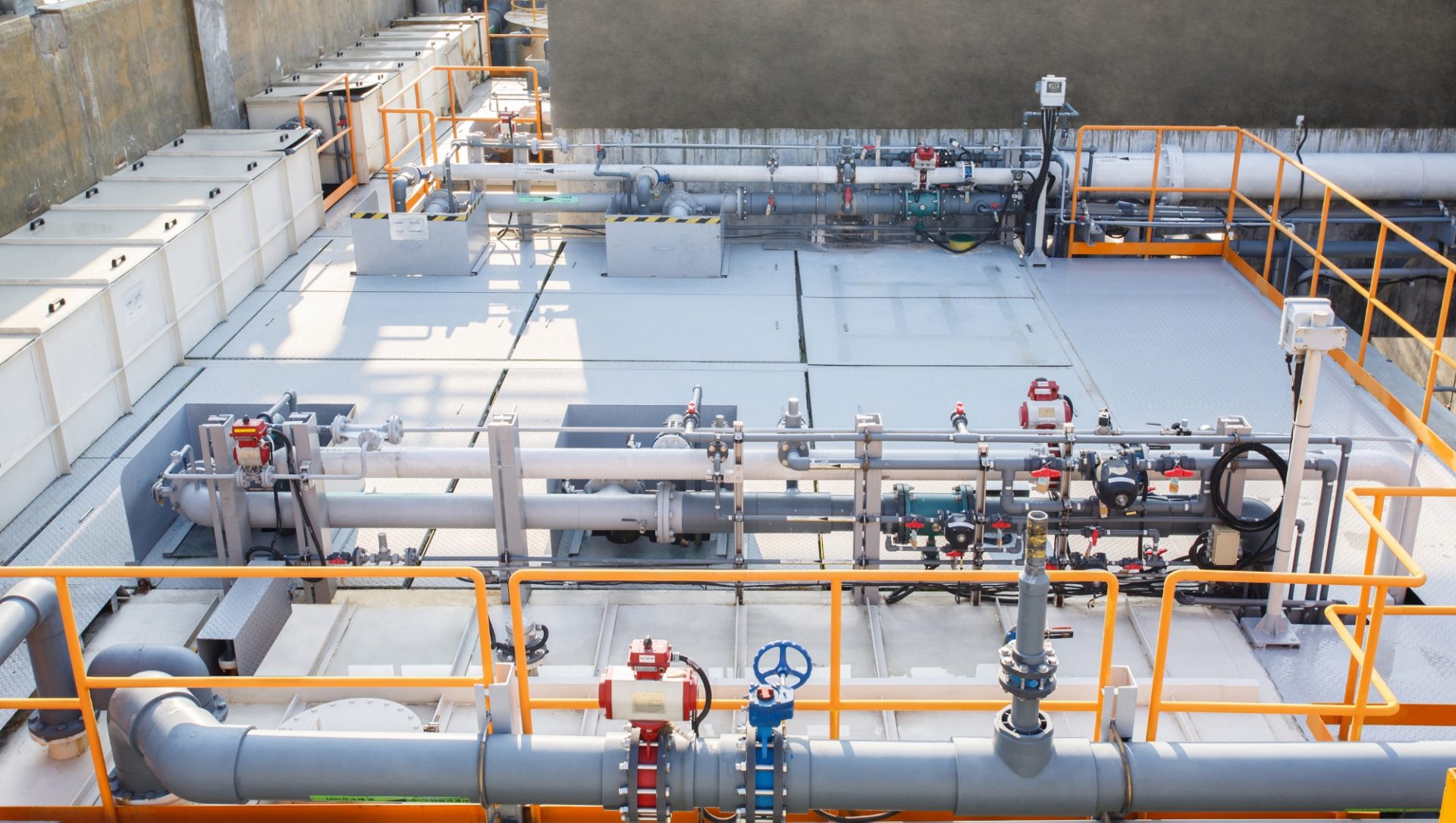
The world is facing crisis and challenges of water shortage due to climate change, whereas the panel industry is an industry that consumes water. Because of the alternation of dry and rainy seasons in Taiwan, the environment contains an uncontrollable risk and impact. Also, regarding the expectation of the residents in the neighborhood, developing manufacturing process of zero discharge of process water on our own is a crucial milestone for the technology industry in Taiwan. Not only does it makes a breakthrough in the existing threshold of water conservation and achieves total water recycling, but also reduces one’s dependence on tap water. Furthermore, it is eco-friendly due to the zero discharge.
( English provided by company. )
Under the impact of extreme weather, the planet encounters water shortage and challenges. Nevertheless, the panel industry is an industry that consumes much water. Also, the alternation between dry and rainy seasons in Taiwan reflects an uncontrollable risk and impact as well. In addition, to meet the expectation of the residents in the neighborhood and to set a good example of striking a balance between the environment and economy, we engaged our path to the development of zero discharge technology.
Development of Optimized Wastewater Separation:
Through water quality analysis, the various ion concentrations in water are captured, so as to separate wastewater for further processing based on the concentration of organisms in the water and the respective attributes. The wastewater in low concentration can be recovered and reused after simple processing, whereas in high concentration it requires multiple computer simulations and adjustments of processing parameters for constant water separation optimization to overcome the challenges of technology threshold and operation costs in reusing high concentration wastewater.
Challenges to the Facilities, Configurations and Operations on Site:
No practice of massive integrated water recycling technology has ever been in place in the technology industry. Through recovery and reuse in phases, the amount of process water required is reduced by 98%, surpassing the conventional process water recycling technology. Moreover, high-efficiency evaporation equipment is employed to achieve the goal of full-recycling of process water.
Overcoming the Greatest Challenge to Ensure a Smooth Manufacturing:
In modifying the system, the plant was still in operation. Apart from managing the existing water consumption and meeting wastewater discharge standards, the progress of new water processing facilities has to be taken care of as well. For instance, the biological treatment via activated sludge process was changed to the process of membrane bio-reactors (MBR) in stages. Meanwhile, wastewater separation, water allocation and water quality monitoring were carried out with prudence, which required adjustment and execution with a close teamwork to complete the whole project.
Benefits
- Approximately 18,000 tons of effluent (equivalent to water consumption of 9.5 standard swimming pools) can all be recycled for use within the plant daily while achieving zero discharge of process water and reducing the environmental load to 0.