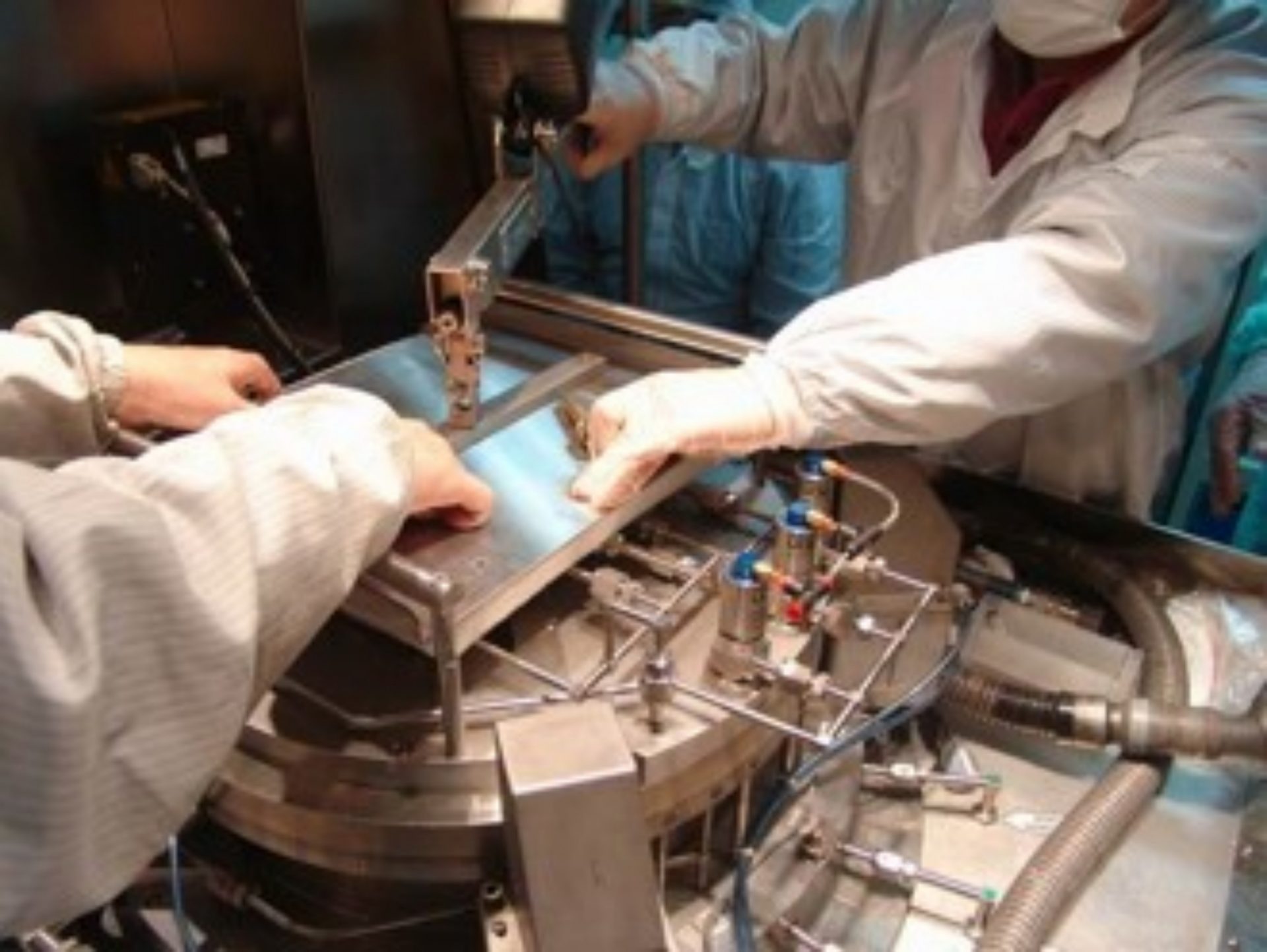
New Up develops key module of Metal Organic Chemical Vapor Deposition (MOCVD) equipment, the gas shower module (Showerhead), which can replace the Showerhead module of the original MOCVD. In the case where equipment manufacturers continue to market a new generation of equipment, the user factories have been deactivating the old type of machine due to the lack of support. These idle old machines can be re-introduced to manufacturing industry after replacing Showerhead with the new type of New Up. With the new type of Showerhead, the production will produce better efficiency and quality, less gas material consumption, extended maintenance intervals and longevity.
( English provided by company. )
MOCVD equipment and key components have depended on foreign suppliers for a long time, which is not conducive to product upgrades and innovative R&D; this affects the competitiveness of domestic optoelectronic industry manufacturers. The Showerhead module is the most important component to determine the production yield of the MOCVD machine. If the current MOCVD equipment is old, it can only be replaced, but the price of a MOCVD machine is high. If it is always necessary to purchase new equipment, it will cost the industry a lot.
Unique Design to Activate the Old Machine
The Showerhead designed and manufactured through the simulation analysis of the heat flow field and the chemical reaction field has a unique double-layer buffer layer and a concentric annular flow channel design structure, which makes the flow field uniform and enhances the epitaxial uniformity. Concentric ring hole arrangement increases the gas retention time period in the reaction chamber,Thus, the gas usage increases and the gas consumption reduces. This structural design shortens the gas diffusion distance, accelerates the reaction rate, and increases the plating rate. That is to say, production efficiency increases. With this uniquely designed Showerhead, the old machine is activated and put into production again to create value.
Software and Hardware Integrated Modules, Equipment Upgrades
The epitaxial process optimization software system is a process parameter prediction software system constructed by multi-physics and chemical simulation analysis with process parameter experiments, calculating optimized simulation analysis data, and then importing a huge database. With the Showerhead hardware, the process of obtaining the process parameters by the epitaxial process personnel is shortened to at least one tenth, and the coating plating rate and the film thickness uniformity are predicted to be more than 95% accuracy.
Benefits
- Reduce gas usage by 10%; extend Showerhead life by 1x