More than 50% of the world’s natural resources are consumed by the construction industry, which is also responsible for 37% of global greenhouse gas emissions. In Europe, the construction sector is particularly resource-intensive, accounting for 50% of raw material consumption, 50% of energy use, 30% of water use, and generating 30% of all waste, while being the source of 40% of carbon emissions. However, under current design practices, only 3–4% of construction waste is reused within buildings. As a result, countries such as the Netherlands and France have prioritized the construction sector in their national circular economy policies as a key industry for transformation.
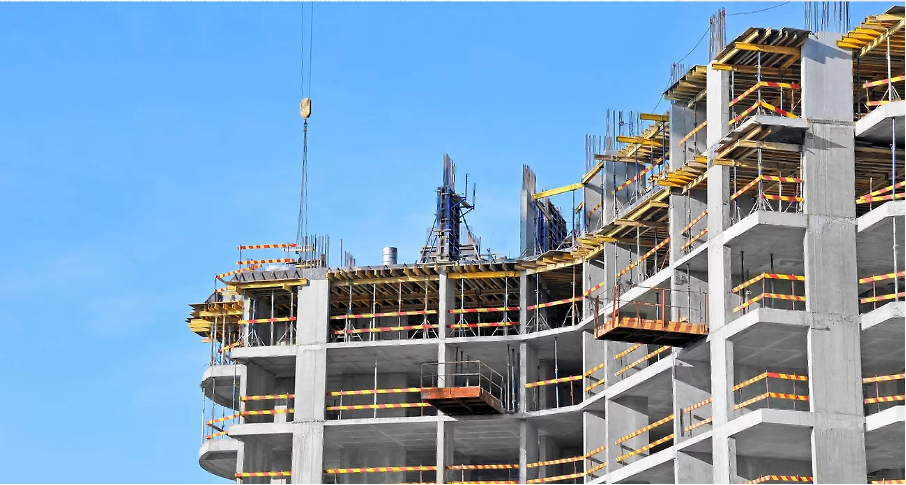
According to United Nations projections, by 2050 the world’s population will reach 9.8 billion, with two-thirds expected to live in urban areas. This will drive a significant increase in building demand, making the sustainable use of the planet’s limited energy and material resources a critical issue. Implementing circular economy principles can effectively reduce the construction sector’s consumption of energy and resources. Through circular design, materials retain their potential for future reuse, enabling true material circularity. At the same time, the circular economy presents new opportunities for the construction industry to upgrade and innovate.
“Circular economy is like a game of Mahjong—the tiles discarded by one player might be just what the next player needs.” —— Zhang Rong-Ji, Director of Land Development, Taiwan Sugar Corporation
A building is a complex assembly of components—structural frames, façades, MEP systems, pipelines, furniture, and appliances—each with its own lifecycle. Without thoughtful planning, these components are often entangled during demolition, leading to destructive teardown methods and vast amounts of construction waste. However, by designing buildings to be adaptable and easy to disassemble, each component can be reused in future projects. In this way, materials shift from being depreciating consumables to appreciating assets—particularly valuable in a resource-constrained future.
Circular buildings aims for zero waste, zero emissions, and zero accidents. It considers the full life cycle of buildings and infrastructure, designing material, water, and energy flows as renewable and recoverable systems, maximizing the value of every resource.
As architect Kuo Ying-Chao from Bio-Architecture Formosana puts it, “Every building should function like a living organism.” Through prefabrication, modularity, and disassembly-friendly design, buildings can be repaired, upgraded, or repurposed at the end of their life cycles—preserving material value and allowing them to become resources for future construction. A building can be analyzed in layers based on the differing lifespans of its systems:
- Structural System:With lifespans of 50–100+ years, structures consume vast resources. Existing structures should be maintained and extended, while new structures should use less material and be modular for future reuse.
- Façade System:Including walls, windows, and roofs, these components last 20–30 years and directly affect building durability and energy use.
- MEP and Pipeline Systems:With 20–30-year lifespans, these are subject to frequent user-driven changes. Exposed piping systems are easier to maintain and replace, reducing overall degradation.
- Interior Partition and Finishing Systems:Lasting 10–20 years, these elements are most frequently altered. Modular materials can increase flexibility and reusability.
- Furniture and Equipment:With shorter lifespans, these can be managed through service-based models, allowing access to high-quality products without ownership burdens.
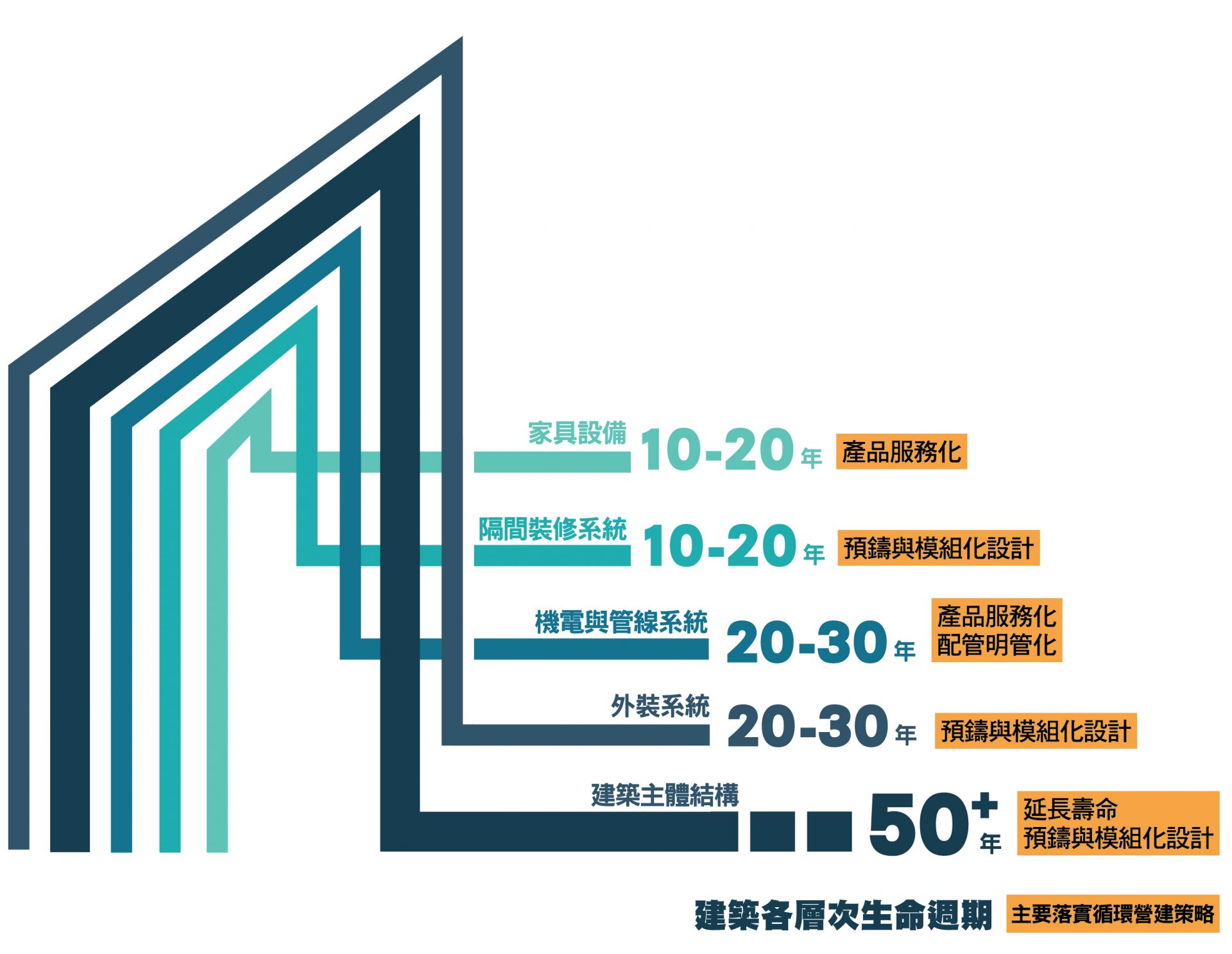
Learn more
The construction and operation of buildings account for 37% of global greenhouse gas emissions: 27% from building operations and 10% from materials. Focusing solely on operational efficiency ignores the substantial emissions tied to the manufacturing and transport of construction materials. Circular strategies can reduce these emissions while improving energy efficiency.
According to the Ellen MacArthur Foundation, applying circular economy principles across design, production, and use could significantly cut demand for steel, aluminum, cement, and plastics in the sector. By 2050, emissions from material processing and construction could fall by 38%, and by extending building lifespans, post-2050 emissions could drop by an additional 56%.
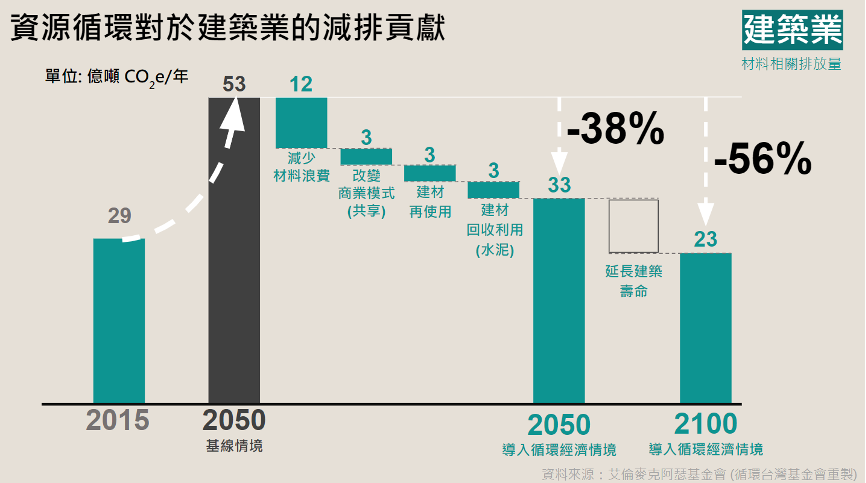
Reducing Material Waste: Potential reduction-1.2 billion tonnes CO₂/year
- Design Inefficiencies
Buildings often overuse materials to exceed safety standards. For example, achieving the same structural strength may require only 50–60% of current cement use. Reducing the cement ratio in concrete or the concrete volume in design can cut emissions significantly. Better specifications, design optimization, and high-performance materials could reduce material waste and lower emissions by 1 billion tonnes annually.
Case:The EcoARK Pavilion - Construction, Renovation, Demolition Waste (These processes generate ~40% of urban waste.)
Techniques like prefabrication, off-site construction, and 3D printing reduce material use and waste while lowering costs. Controlled off-site construction can reduce waste by up to 90% compared to on-site methods.
Case:The Holland Pavilion
Shifting Business Models: Potential reduction-300 million tonnes CO₂/year
Building usage rates are often low. In Europe, even during office hours, 60% of office space is unused; in the UK, 49% of homes have at least two unoccupied rooms. Service-based circular models—such as P2P rentals and coworking spaces—can maximize space and equipment use.
Case:Taisugar Circular Village、Color Park International
Learn more:藏在地毯裡的「循環商機」
Reuse of Building Materials: Potential reduction-300 million tonnes CO₂/year
Only 20–30% of construction waste is currently recycled, largely due to poor design and lack of material information. Designing for disassembly and reuse maximizes material value and reduces demand for new materials. In Shalun Circular Park, 41% of steel components can be reused. Recent steel price increases—up 40% in five years—highlight the asset value of stored materials.
Recycling Construction Materials: Potential reduction-300 million tonnes CO₂/year
Recycling construction materials can reduce emissions by 40–70% compared to producing virgin materials. Cement and plastics still lag behind steel in recyclability. Designing for deconstruction, increasing recyclable volumes, and improving recycled material quality are essential.
Extending Building Lifespan: Potential reduction (post-2050)-1 billion tonnes CO₂/year
While buildings can last 50–100 years, many are demolished after 20–30 due to inflexible design. Modular, durable, and repairable designs can extend use and reduce emissions. Modular construction allows up to 80% material reuse, and the carbon reduction impact continues well beyond 2050.
《Energy Performance of Buildings Directive》EPBD
Effective from May 28, 2024, this directive aims to achieve zero-emission buildings by 2050 through:
- Stricter standards for new buildings and life-cycle carbon assessments
- More reliable energy performance certificates
- One-stop renovation services
- Enhanced data collection and sharing
《Construction Products Regulation》CPR
Approved in April 2024, this regulation:
- Introduces new, harmonized requirements for construction products
- Ensures products are more durable, repairable, recyclable, and easier to remanufacture
- Leverages digital product passports to reduce administrative burdens
200,000 Public Housing Units—Driving a Low-Carbon Construction Shift
The residential and commercial sectors account for nearly 20% of Taiwan’s total emissions, second only to manufacturing. High energy use in existing buildings makes this sector key to achieving Taiwan’s 2025 reduction targets.
Taiwan’s plan to build 200,000 public housing units in eight years is entering its second phase. Nearly 70,000 units are expected in the coming years. Under traditional construction methods, this would consume 12.5 million tonnes of raw materials—equivalent to 17 Taipei 101 towers—and generate the same amount of waste. However, if the Ministry of the Interior uses this opportunity to implement circular construction, it could fulfill housing justice goals while aligning with net-zero emissions policies and driving industry-wide transformation.
Further Reading:
Digital Twins for Buildings
Building Information Modeling (BIM), a mature technology in the construction sector, enables detailed digital passports for each material used in a building—creating a "digital twin." Buildings can then be seen as temporary material banks, with components reused in future projects once the building is decommissioned.
Developing Local Low-Carbon Materials
Taiwan's construction industry heavily relies on reinforced concrete, consuming over 10 million tonnes of cement annually. Both cement and steel are highly carbon-intensive. Future trends will require a rethinking of the material sector. Efforts are already underway to increase the use of alternative materials and invest in cement recycling technologies.
In addition, emerging low-carbon building materials—such as domestically sourced timber, which sequesters carbon during growth, and alternatives like bamboo or mushroom-based composites—offer innovative solutions with reduced transportation emissions.